In the dynamic landscape of manufacturing, distribution, and logistics, efficiency reigns supreme. As industries strive for streamlined processes and enhanced productivity, automatic separating and sorting equipment emerges as a vital ally. These sophisticated systems boast the ability to swiftly categorize, organize, and distribute items with precision. But how do we gauge their efficiency? Enter key performance indicators (KPIs), the compass guiding us toward optimal performance and operational excellence.
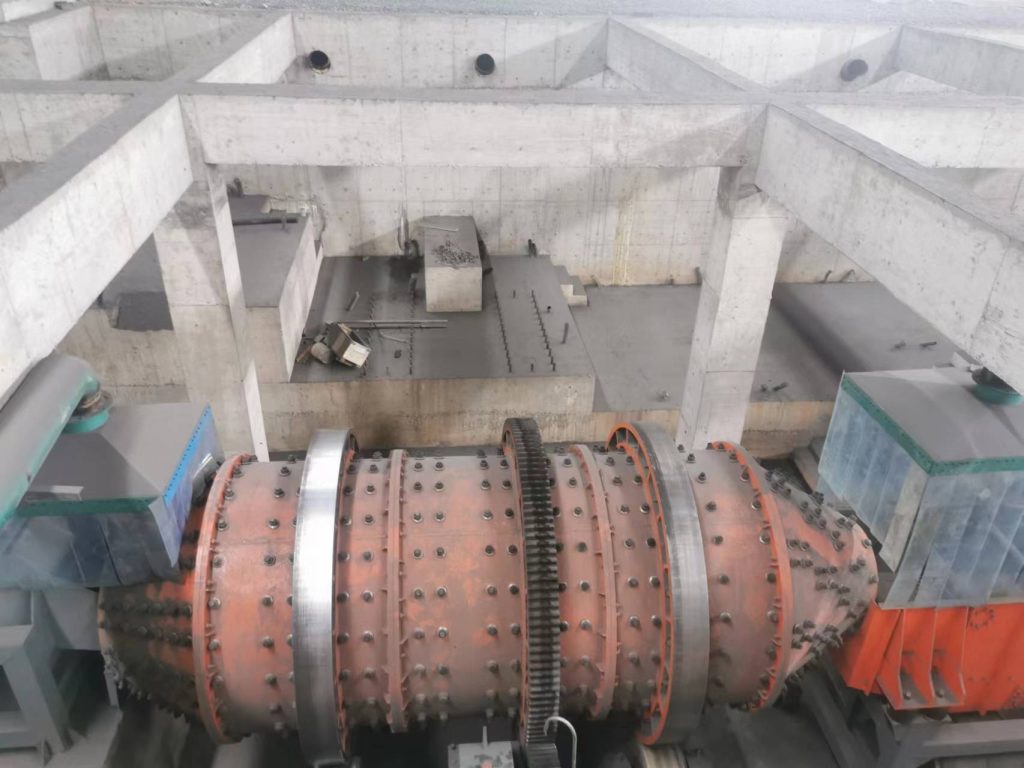
Throughput
At the heart of assessing automatic separating and sorting equipment lies throughput—the pulse of productivity. Throughput measures the rate at which items flow through the system, reflecting its capacity to handle a high volume of items efficiently. A robust throughput indicates that the equipment is firing on all cylinders, processing items swiftly and seamlessly.
Accuracy
In the realm of sorting and categorization, accuracy is king. This KPI evaluates the equipment’s ability to identify, separate, and sort items according to predefined criteria. A high accuracy rate signifies precision and reliability in the sorting process, minimizing errors and ensuring that items reach their designated destinations with pinpoint accuracy.
Sorting Speed
Time is of the essence in the world of automatic sorting. Sorting speed measures how quickly the equipment can categorize items based on specific attributes such as size, shape, color, or weight. A rapid sorting speed is indicative of efficiency, enabling the equipment to process items swiftly and keep pace with demanding operational requirements.
Maintenance Downtime
Even the most advanced equipment requires periodic maintenance and upkeep. Maintenance downtime quantifies the amount of time the equipment is out of operation for maintenance, repairs, or cleaning. Minimizing maintenance downtime is essential for maximizing operational uptime, ensuring continuous operation, and optimizing productivity.
Error Rates
In a realm where precision is paramount, error rates serve as a critical benchmark. This KPI measures the frequency of incorrect sorts, misidentifications, or failures in the sorting process. By monitoring and reducing error rates, operators can enhance the reliability and accuracy of the equipment, mitigating disruptions and optimizing overall efficiency.
Utilization Rate
Efficiency isn’t just about speed—it’s also about utilization. The utilization rate measures the percentage of time that the equipment is actively sorting and processing items compared to its total available operating time. A high utilization rate indicates optimal use of the equipment’s capacity and resources, maximizing efficiency and productivity.
Energy Efficiency
In an era of sustainability, energy efficiency takes center stage. This KPI quantifies the amount of energy consumed by the equipment to operate and sort items. By improving energy efficiency, operators can not only reduce operational costs but also minimize their environmental footprint, contributing to a greener, more sustainable future.
In conclusion, the efficiency of automatic separating and sorting equipment is multifaceted, encompassing various key performance indicators that collectively determine its effectiveness and reliability. By monitoring and optimizing these KPIs, operators and managers can unlock the full potential of their equipment, driving operational excellence, and staying ahead in today’s fast-paced business landscape.