Automatic heat treatment lines are pivotal assets in industrial environments, playing a crucial role in enhancing the mechanical properties of materials. To uphold their efficiency and reliability, meticulous maintenance and precise calibration procedures are imperative. Let's delve into the comprehensive strategies for ensuring the optimal performance of these automated systems.
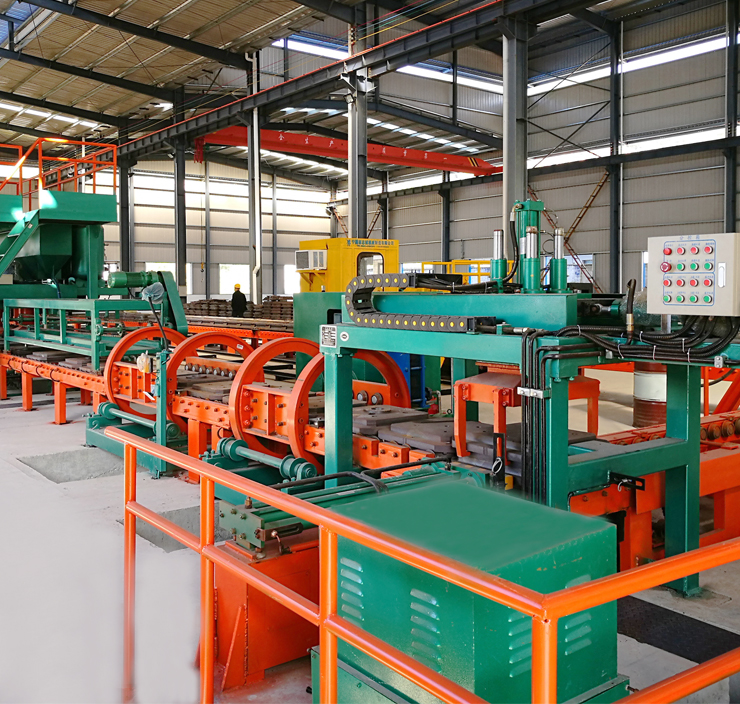
Routine Inspections and Cleaning:
Regular inspections form the cornerstone of proactive maintenance, encompassing thorough checks and cleaning protocols:
- Component Examination: Conducting visual and functional assessments of conveyor belts, sensors, heating elements, and control systems to detect any signs of wear, damage, or malfunction.
- Cleaning Regimen: Regularly removing debris and contaminants from equipment surfaces to prevent performance degradation and ensure optimal functionality.
Scheduled Maintenance Tasks:
Establishing a structured maintenance schedule tailored to manufacturer recommendations and equipment specifications is paramount for long-term performance:
1. Lubrication Management: Applying appropriate lubricants to moving parts minimizes friction, reduces wear, and extends component lifespan.
2. Temperature Calibration: Periodic calibration of temperature sensors and controllers guarantees precise and consistent heat treatment processes, maintaining product quality and performance standards.
3. Belt Tension Adjustment: Optimizing conveyor belt tension prevents slippage, ensures smooth material handling, and enhances overall system efficiency.
4. Electrical Systems Evaluation: Regular checks of electrical connections, wiring integrity, and safety features mitigate risks, promote operational safety, and minimize downtime due to electrical failures.
Calibration Procedures:
Accurate calibration is pivotal in upholding the precision and reliability of automatic heat treatment lines, encompassing key calibration procedures:
1. Thermocouple Verification: Comparing temperature readings against established standards and adjusting calibration settings as needed to maintain accuracy and consistency.
2. PID Controller Optimization: Fine-tuning Proportional-Integral-Derivative (PID) control parameters ensures optimal temperature control, stability, and energy efficiency.
3. Conveyor Speed Alignment: Verifying and adjusting conveyor speed settings to uphold consistent heat treatment times, product quality, and throughput rates.
4. Safety System Validation: Rigorous testing of safety interlocks, emergency stop mechanisms, and alarm systems ensures compliance with safety standards, mitigates risks, and safeguards personnel and equipment.
The diligent implementation of regular maintenance and precise calibration protocols is instrumental in maximizing the efficiency, reliability, and safety of automatic heat treatment lines. By prioritizing these proactive measures, operators can extend equipment lifespan, minimize downtime, uphold product quality standards, and optimize overall operational performance in industrial heat treatment applications.