ในโลกของการขุดและการสี การแยกและการจัดการลูกบดอย่างเหมาะสมถือเป็นสิ่งสำคัญในการรักษาประสิทธิภาพ ลดระยะเวลาหยุดทำงาน และเพิ่มประสิทธิภาพต้นทุนการดำเนินงาน ลูกบดที่ใช้ในเครื่องบดลูกบดสำหรับบดแร่ แร่ธาตุ และวัสดุอื่นๆ เป็นส่วนประกอบสำคัญในกระบวนการอุตสาหกรรมต่างๆ มากมาย เมื่อเวลาผ่านไป ลูกบดเหล่านี้จะสึกกร่อน เสื่อมสภาพ หรือผสมกับวัสดุที่ไม่ต้องการ ซึ่งอาจส่งผลกระทบเชิงลบต่อประสิทธิภาพการบดและคุณภาพของผลิตภัณฑ์ขั้นสุดท้าย
เพื่อแก้ไขปัญหาเหล่านี้ อุปกรณ์แยกลูกบด มีบทบาทสำคัญ อุปกรณ์นี้ช่วยแยกลูกบดที่สึกหรอออกจากวัสดุที่กำลังประมวลผล จึงป้องกันการปนเปื้อน ปรับปรุงกระบวนการบด และประหยัดต้นทุนวัสดุบด
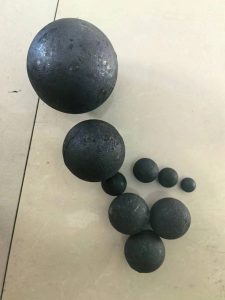
อุปกรณ์แยกลูกบดคืออะไร?
อุปกรณ์แยกลูกบดหมายถึงเครื่องจักรเฉพาะทางที่ออกแบบมาเพื่อแยกลูกบดออกจากวัสดุอื่นในเครื่องบดโดยอัตโนมัติหรือกึ่งอัตโนมัติ ระบบเหล่านี้มักจะรวมเทคนิคการแยกด้วยกลไก แม่เหล็ก หรืออากาศ เพื่อดึงลูกบดที่มีค่าออกมาและกรองเศษวัสดุและสารแปลกปลอมออกไป
อุปกรณ์ดังกล่าวมีความจำเป็นในอุตสาหกรรมต่างๆ เช่น การทำเหมืองแร่ การผลิตปูนซีเมนต์ และ การรีไซเคิลที่ใช้ลูกบดจำนวนมากและจำเป็นต้องเปลี่ยนเป็นประจำ ลูกบดซึ่งมักทำด้วยเหล็กมีความทนทานแต่จะเสื่อมสภาพลงเมื่อเวลาผ่านไป จึงต้องใช้กระบวนการแยกที่อนุญาตให้ การรีไซเคิล และ การนำกลับมาใช้ใหม่.
ความสำคัญของการแยกลูกบด
1. เพิ่มประสิทธิภาพการบด
หากไม่แยกลูกบดอย่างถูกต้อง ชิ้นส่วนลูกบดที่แตกและมีขนาดเล็กจะปะปนกับแร่หรือวัสดุอื่นที่กำลังประมวลผล ส่งผลให้ประสิทธิภาพการบดลดลงและใช้พลังงานมากขึ้น การแยกลูกบดที่สึกหรอหรือเสียหายออกทำให้มั่นใจได้ว่าจะใช้ลูกบดที่มีขนาดเหมาะสมเท่านั้น จึงช่วยรักษา การบดที่มีประสิทธิภาพ.
2. การประหยัดต้นทุน
ลูกบดเป็นวัสดุสิ้นเปลืองที่มีราคาแพง และการเปลี่ยนลูกบดอยู่ตลอดเวลาอาจทำให้มีต้นทุนการดำเนินงานที่สูง ธุรกิจต่างๆ สามารถประหยัดค่าใช้จ่ายในการซื้อสื่อใหม่ได้อย่างมาก โดยการนำลูกบดที่ยังอยู่ในสภาพดีกลับมาใช้ใหม่ การรีไซเคิลลูกบดและอุปกรณ์แยกที่เหมาะสมยังช่วยลดความต้องการสื่อบดใหม่ได้ ทำให้ต้นทุนโดยรวมลดลงด้วย
3. การลดการปนเปื้อน
ในอุตสาหกรรมที่ความบริสุทธิ์ของผลิตภัณฑ์เป็นสิ่งสำคัญ เช่น อุตสาหกรรมอาหาร ยา และเคมี การมีอนุภาคแปลกปลอม เช่น ลูกบดที่แตกหัก อาจทำให้เกิดการปนเปื้อนได้ ระบบแยกลูกบดจะช่วยลดความเสี่ยงนี้ลงโดยคัดแยกวัตถุแปลกปลอมออกอย่างมีประสิทธิภาพ ทำให้มั่นใจได้ว่าผลิตภัณฑ์จะมีคุณภาพสูงขึ้น
4. ปรับปรุงความปลอดภัยและการบำรุงรักษา
การจัดการลูกบด โดยเฉพาะลูกบดขนาดใหญ่หรือสึกหรอ อาจเป็นอันตรายต่อผู้ปฏิบัติงานได้ ระบบอัตโนมัติหรือกึ่งอัตโนมัติ ระบบแยกลูกบด ลดการจัดการด้วยมือ ลดอุบัติเหตุและการบาดเจ็บ ระบบเหล่านี้ยังช่วยป้องกันเศษลูกบดไม่ให้ไปทำลายอุปกรณ์อื่น ลดโอกาสในการซ่อมแซมราคาแพงและระยะเวลาหยุดทำงานโดยไม่ได้วางแผน
ประเภทของอุปกรณ์แยกลูกบด
มีหลายประเภท อุปกรณ์แยกลูกบด มีให้เลือกใช้ โดยแต่ละแบบออกแบบมาเพื่อตอบสนองความต้องการในการใช้งานที่เฉพาะเจาะจง ด้านล่างนี้เป็นประเภทที่พบได้บ่อยที่สุด:
1. เครื่องแยกแม่เหล็ก
การแยกด้วยแม่เหล็กเป็นหนึ่งในวิธีที่ได้รับความนิยมมากที่สุดในการแยกลูกบดออกจากวัสดุที่กำลังประมวลผล เครื่องแยกด้วยแม่เหล็กใช้แม่เหล็กที่มีพลังในการดึงดูดลูกบดที่มีธาตุเหล็ก ทำให้สามารถแยกลูกบดออกจากวัสดุที่ไม่มีธาตุเหล็กได้ เครื่องแยกด้วยแม่เหล็กมี 2 รูปแบบหลัก ได้แก่ เครื่องแยกด้วยแม่เหล็กแบบเปียกและเครื่องแยกด้วยแม่เหล็กแบบแห้ง
การแยกด้วยแม่เหล็กมีประสิทธิภาพสูงมากในอุตสาหกรรมต่างๆ เช่น อุตสาหกรรมการทำเหมืองแร่ ซึ่งมักใช้ลูกบดเหล็ก
2. เครื่องจำแนกอากาศ
เครื่องแยกอากาศใช้ลมความเร็วสูงเพื่อแยกลูกบดออกจากวัสดุละเอียด ลูกบดที่มีน้ำหนักมากจะตกลงไปในถังเก็บในขณะที่อนุภาคที่มีน้ำหนักเบากว่าจะถูกพัดพาไปด้วยกระแสลม วิธีการนี้มักใช้ในอุตสาหกรรมต่างๆ เช่น การผลิตปูนซีเมนต์และการแปรรูปผง ซึ่งจำเป็นต้องแยกให้ละเอียด
3. เครื่องแยกแบบสั่นสะเทือน
เครื่องแยกแบบสั่นใช้การสั่นสะเทือนเพื่อช่วยแยกลูกบดออกจากวัสดุที่ละเอียดกว่า เครื่องแยกประเภทนี้ประกอบด้วยตะแกรงหรือตาข่ายที่สั่น ทำให้อนุภาคขนาดเล็กผ่านเข้าไปได้ในขณะที่ลูกบดขนาดใหญ่ยังคงอยู่ด้านบน เครื่องแยกแบบสั่นเหมาะอย่างยิ่งสำหรับการแยกลูกบดออกจากส่วนผสมของอนุภาคขนาดเล็กหรือเศษวัสดุอื่นๆ
4. เครื่องแยกแรงโน้มถ่วง
การแยกด้วยแรงโน้มถ่วงนั้นอาศัยความแตกต่างของความหนาแน่นระหว่างลูกบดกับวัสดุอื่นๆ ลูกบดที่มีน้ำหนักมากจะถูกแยกออกจากวัสดุที่มีน้ำหนักเบากว่าโดยใช้แรงโน้มถ่วง ทำให้วิธีนี้เหมาะอย่างยิ่งสำหรับการดำเนินงานขนาดใหญ่ เช่น ในอุตสาหกรรมเหมืองแร่
5. ระบบแยกสารด้วยมือ
สำหรับธุรกิจขนาดเล็กหรือธุรกิจที่คำนึงถึงงบประมาณ ระบบการแยกด้วยมืออาจยังคงใช้ได้ ระบบเหล่านี้เกี่ยวข้องกับตะแกรงหรือตะแกรงกรอง ซึ่งผู้ปฏิบัติงานจะแยกลูกบดออกจากวัสดุอื่นด้วยมือ แม้ว่าจะใช้แรงงานมากกว่า แต่การแยกด้วยมือก็คุ้มต้นทุนสำหรับธุรกิจที่มีปริมาณงานน้อยกว่า
ปัจจัยที่ต้องพิจารณาเมื่อเลือกอุปกรณ์แยกลูกบด
เมื่อเลือกสิ่งที่ดีที่สุด อุปกรณ์แยกลูกบด, พิจารณาปัจจัยต่อไปนี้:
1. ประเภทของวัสดุที่กำลังประมวลผล
วัสดุที่กำลังประมวลผลมีอิทธิพลต่อวิธีการแยกที่จะได้ผลดีที่สุด ตัวอย่างเช่น เครื่องจำแนกอากาศ หรือ เครื่องแยกแบบสั่นสะเทือน เหมาะสำหรับวัสดุที่มีอนุภาคละเอียดจำนวนมาก ตัวคั่นแม่เหล็ก เหมาะอย่างยิ่งสำหรับการแยกลูกบดเหล็กในเหมือง
2. ขนาดและประเภทของลูกบอล
ลูกบดมีหลายขนาดและวัสดุ เช่น ลูกเหล็กหรือโลหะผสมโครเมียมสูง อุปกรณ์จะต้องรองรับประเภทและขนาดที่แตกต่างกันเหล่านี้ ระบบบางระบบได้รับการออกแบบมาโดยเฉพาะสำหรับลูกบดขนาดเล็กหรือขนาดใหญ่ ในขณะที่ระบบอื่นๆ สามารถจัดการกับลูกบดขนาดต่างๆ ได้
3. ความสามารถในการรับส่งข้อมูล
สำหรับการดำเนินการขนาดใหญ่ ความสามารถในการรับส่งข้อมูลถือเป็นปัจจัยสำคัญที่ต้องพิจารณา ระบบการแยกจะต้องรองรับปริมาณลูกบดและวัสดุที่ต้องประมวลผลภายในกรอบเวลาที่กำหนด ซึ่งถือเป็นสิ่งสำคัญในอุตสาหกรรมต่างๆ เช่น การทำเหมืองหรือการผลิตปูนซีเมนต์ ที่ต้องผลิตในปริมาณมาก
4. ระบบอัตโนมัติเทียบกับการจัดการด้วยมือ
ระบบอัตโนมัติมีประสิทธิภาพมากกว่าและมีต้นทุนแรงงานต่ำกว่า แต่ระบบแมนนวลอาจคุ้มทุนกว่าสำหรับการดำเนินงานขนาดเล็ก การตัดสินใจเลือกระหว่างระบบอัตโนมัติเต็มรูปแบบและกึ่งอัตโนมัติขึ้นอยู่กับขนาดของการดำเนินงาน
5. ค่าใช้จ่ายและการบำรุงรักษา
พิจารณาต้นทุนเริ่มต้นของอุปกรณ์แยกรวมถึงความต้องการการบำรุงรักษาอย่างต่อเนื่อง ระบบอัตโนมัติอาจมีต้นทุนล่วงหน้าที่สูงกว่า แต่สามารถนำไปสู่การประหยัดในระยะยาวได้อย่างมากเนื่องจากมีประสิทธิภาพและระยะเวลาหยุดทำงานที่ลดลง

อุปกรณ์แยกลูกบด มีความสำคัญอย่างยิ่งต่อการเพิ่มประสิทธิภาพกระบวนการบด ลดต้นทุนการดำเนินงาน และปรับปรุงคุณภาพผลิตภัณฑ์ ด้วยเทคโนโลยีการแยกสารที่หลากหลาย เช่น เครื่องแยกแม่เหล็ก เครื่องแยกอากาศ และเครื่องแยกแบบสั่นสะเทือน อุตสาหกรรมต่างๆ สามารถเลือกโซลูชันที่ดีที่สุดตามความต้องการเฉพาะของตนได้ ไม่ว่าคุณจะอยู่ในอุตสาหกรรมเหมืองแร่ การผลิตปูนซีเมนต์ หรือการรีไซเคิล การลงทุนในอุปกรณ์แยกสารที่เหมาะสมถือเป็นสิ่งสำคัญในการรักษาประสิทธิภาพการดำเนินงานและเพิ่มผลกำไรสูงสุด
โดยการดำเนินการตามความเหมาะสม ระบบแยกลูกบดธุรกิจต่างๆ สามารถมั่นใจได้ว่าการดำเนินงานจะราบรื่นขึ้น ลดความเสี่ยงในการปนเปื้อน และยืดอายุการใช้งานของลูกบด ซึ่งสุดท้ายแล้วก็จะปรับปรุงประสิทธิภาพการผลิตและประหยัดต้นทุน