In the world of industrial grinding, the quality of grinding balls plays a pivotal role in determining milling performance. As the primary media for reducing particle size in various applications, grinding balls directly impact the efficiency and effectiveness of the milling process. This article delves into the connection between grinding ball quality and milling performance, highlighting the significant impact it has on the overall operation.
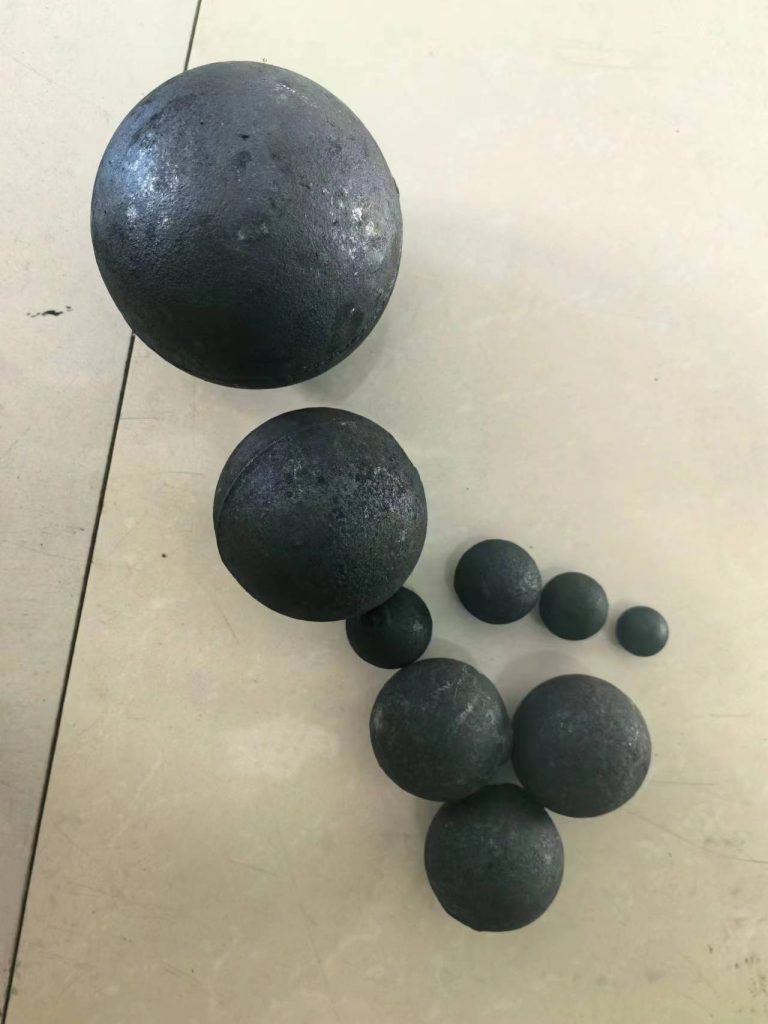
Consistent Particle Size Reduction
Grinding Ball Quality: High-quality grinding balls exhibit uniform shape, size, and hardness, ensuring consistent particle size reduction during milling.
Enhanced Milling Efficiency: Uniform particle size distribution achieved through the use of quality grinding balls leads to improved milling efficiency and product quality.
Reduced Energy Consumption
Optimized Grinding Ball Design: Well-designed grinding balls with appropriate hardness and composition require less energy to break down particles, reducing overall energy consumption.
Efficient Milling Process: Lower energy consumption translates into higher milling efficiency and cost savings, making quality grinding balls a vital component in achieving sustainable operations.
Increased Milling Capacity
Wear Resistance: High-quality grinding media balls exhibit superior wear resistance, allowing for extended operational life and increased milling capacity.
Reduced Downtime: Longer-lasting grinding balls minimize the need for frequent replacements, reducing downtime and maximizing production output.
Improved Grinding Efficiency
Effective Impact and Crushing: Quality grinding balls possess the necessary hardness and impact resistance to efficiently crush and grind particles, resulting in improved grinding efficiency.
Reduced Overgrinding: With precise control over grinding ball quality, the risk of overgrinding is minimized, ensuring optimal particle size distribution and maximizing resource utilization.
Enhanced Product Quality
Minimal Contamination: High-quality grinding balls are free from impurities and contaminants, preventing cross-contamination and ensuring the purity and integrity of the milled product.
Consistent Performance: Quality grinding balls offer consistent performance, resulting in uniform product quality and meeting the required specifications.
Integration of Technology in Grinding Ball Production and Usage
The integration of technology in grinding ball production and usage has transformed the industry. Advanced data analytics and sensors now enable real-time monitoring of grinding ball performance, providing valuable insights into wear rates, impact forces, and overall efficiency. This technological integration empowers industries to optimize their milling processes, minimize downtime, and enhance productivity through informed decision-making.
Sustainable Practices in Grinding Ball Manufacturing
Many companies are embracing sustainable initiatives in grinding ball manufacturing by focusing on eco-friendly materials and production methods. This shift towards sustainability not only reduces environmental impact but also aligns with the growing emphasis on environmentally conscious practices within the industry. Utilizing recycled materials and implementing energy-efficient manufacturing processes are leading to more sustainable grinding ball production.
The connection between grinding ball quality and milling performance is undeniable. By recognizing the critical role of grinding ball quality, industries can unlock the full potential of their milling processes, leading to improved efficiency, cost savings, and superior product outcomes. It's great to see how crucial the quality of grinding balls is in industrial grinding processes. With the integration of technology, sustainable practices, and real-world success stories, the industry is poised for continuous advancement and innovation.