In today's fast-paced industrial landscape, automation is leading the charge in enhancing manufacturing efficiency. Automatic heat treatment lines are transforming industries by offering faster, more precise, and cost-effective solutions for heat treating metals and alloys. This comprehensive guide explores the significance of automatic heat treatment lines, their components, benefits, and how they impact various industries.
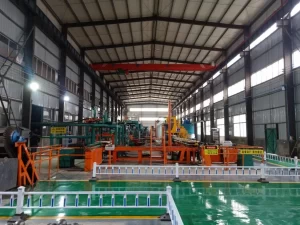
What is an Automatic Heat Treatment Line?
An automatic heat treatment line refers to an advanced industrial system designed for the heat treatment of metals or alloys. This process involves heating materials to specific temperatures followed by controlled cooling to achieve optimal physical and chemical properties. Automated heat treatment systems provide superior precision, consistency, and efficiency compared to manual methods.
Why are Automatic Heat Treatment Lines Essential?
The demand for high-quality, precision-engineered components across industries such as automotive, aerospace, and manufacturing is rapidly increasing. Automated heat treatment systems are vital for meeting these demands. Here’s why:
- Increased Efficiency: Automation speeds up the entire heat treatment process, reducing cycle times and boosting production throughput.
- Precision and Consistency: Automated controls ensure uniformity and consistency in heat treatment, reducing errors and variability.
- Cost-Effectiveness: By reducing labor costs and minimizing human error, automatic heat treatment lines are a cost-effective solution in the long run.
- Scalability: These systems can easily be scaled to meet higher production volumes, making them ideal for growing businesses.
Key Components of an Automatic Heat Treatment Line
An automatic heat treatment line includes several key components, all of which work together to ensure a smooth and efficient process. These components ensure the heat treatment is done with precision and accuracy.
1. Loading and Unloading Systems
Automated loading and unloading systems help move materials in and out of the furnace or heat treatment chambers. This ensures a continuous, non-stop workflow while minimizing human intervention.
2. Heating Zone
The heating zone is where materials are brought up to the required temperatures. This is typically achieved using induction heaters or high-temperature furnaces. Precision temperature control is critical for achieving the desired properties in the treated materials.
3. Quenching and Cooling Systems
Once the material has reached the necessary temperature, it is rapidly cooled using methods like water, oil, or air quenching. This cooling process hardens the material and is key to achieving specific mechanical properties such as increased tensile strength or wear resistance.
4. Control and Monitoring Systems
Control systems are the brains of the automatic heat treatment line. These systems use advanced sensors and real-time data to monitor variables like temperature, cooling rate, and time. By adjusting these parameters, the system ensures that each batch is treated to the exact specifications.
5. Robotic and Handling Systems
Robotic arms and conveyors handle materials as they move through the different stages of heat treatment. These systems reduce human labor, improve safety, and increase speed by seamlessly transferring materials.
6. Cooling/Conveyor Systems
Conveyor belts and cooling systems ensure the parts move smoothly from one stage to the next while undergoing necessary temperature changes.
Types of Automatic Heat Treatment Lines
When it comes to automatic heat treatment lines, manufacturers generally choose between batch heat treatment lines and continuous heat treatment lines. Both systems have their advantages depending on the production requirements.
Batch Heat Treatment Lines
In batch heat treatment lines, parts are treated in groups, which is ideal for smaller runs or varied materials. This type of system allows manufacturers to process a wide range of materials with different heat treatment needs.
Continuous Heat Treatment Lines
A continuous heat treatment line treats materials in a continuous stream, making it highly efficient for large-scale production. Parts move through the system automatically, making this ideal for high-volume applications, such as automotive manufacturing.
Key Benefits of Automatic Heat Treatment Lines
Adopting an automatic heat treatment line offers several key benefits:
1. Enhanced Precision and Consistency
Automated heat treatment ensures each part receives the exact treatment it needs. The use of sensors and controls guarantees uniformity across production runs, resulting in consistent quality.
2. Reduced Labor Costs
By automating repetitive tasks, manufacturers can significantly reduce their labor costs. Automation also minimizes the risk of human error during handling or treatment, ensuring higher quality outputs.
3. Improved Efficiency and Increased Throughput
Automation accelerates the heat treatment process, which leads to higher production rates and reduced cycle times. This is essential for businesses needing to meet tight deadlines and large orders.
4. Flexibility and Customization
Modern automatic heat treatment lines can be customized to accommodate various materials and production needs. Whether it’s for high-performance aerospace parts or automotive components, these systems can adapt to specific requirements.
5. Energy Efficiency
Automated systems are optimized for energy usage, reducing energy consumption and costs while improving overall efficiency.
Industries That Benefit from Automatic Heat Treatment Lines
Automatic heat treatment lines are critical in several industries that demand high-quality materials with precise mechanical properties.
1. Automotive Industry
The automotive industry benefits from automatic heat treatment lines for the production of gears, shafts, engine components, and more. Heat-treated parts offer enhanced durability and performance in demanding automotive applications.
2. Aerospace Industry
In the aerospace sector, automatic heat treatment lines are used to treat turbine blades, landing gear, and other critical components that must meet stringent safety and performance standards.
3. Tool Manufacturing
Heat-treated cutting tools, dies, and molds are essential in tool manufacturing. Automated systems allow for precise control of hardness and toughness, ensuring high-quality products.
4. Steel and Metallurgical Industries
Steel manufacturers use automatic heat treatment lines to process metal parts for various applications. These lines ensure consistent material properties like hardness, toughness, and tensile strength across large-scale production runs.
Why Automatic Heat Treatment Lines Are the Future of Industrial Processing
In an era of increased demand for high-quality and cost-effective production, automatic heat treatment lines are quickly becoming the industry standard. These systems offer unparalleled precision, consistency, and scalability, enabling manufacturers to meet the high standards of modern industries.
By investing in an automatic heat treatment line, companies can enhance their production capabilities, reduce labor costs, and ensure top-quality outcomes that meet the ever-evolving needs of global markets.