Grinding balls are essential components in various industrial processes, serving as the key element in reducing solid materials into fine powders or slurries. The meticulous manufacturing process of grinding balls encompasses several crucial stages, commencing from the sourcing of raw materials to the comprehensive inspection of the finished product. Let's delve into the intricate journey of how grinding balls are meticulously crafted from start to finish.
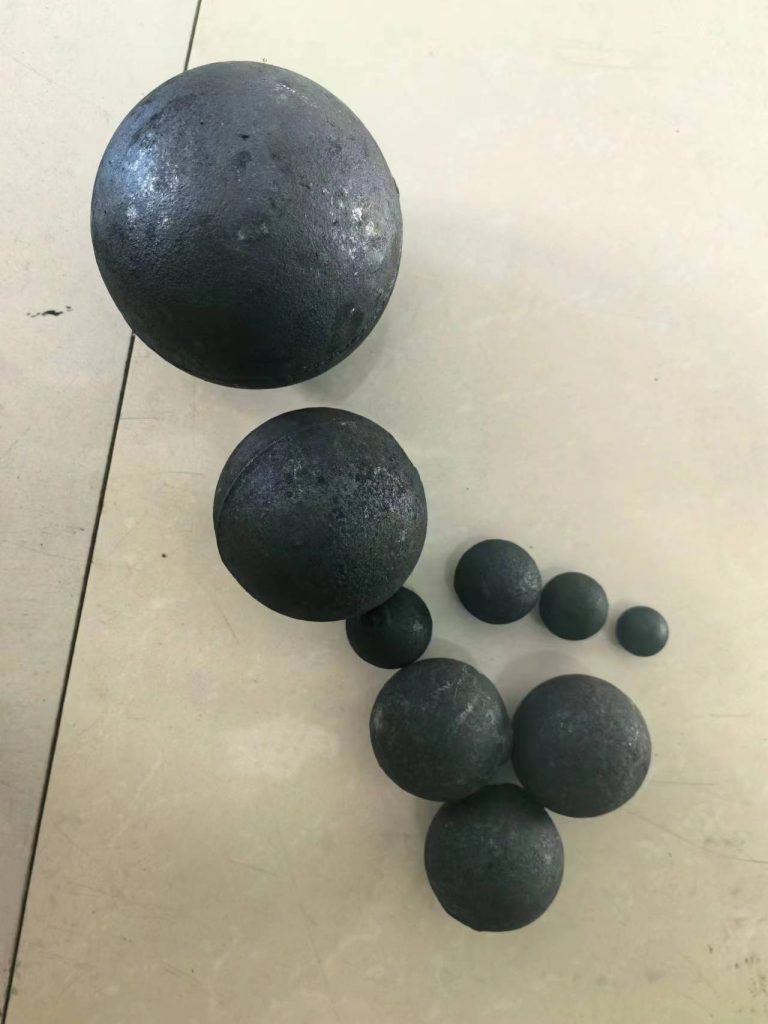
Raw Material Sourcing and Evaluation:
The manufacturing process commences with the careful selection and procurement of raw materials, primarily steel and alloy additives such as chromium. These materials are chosen for their exceptional strength and durability, ensuring the production of high-performance grinding balls. Reputable suppliers are engaged to guarantee the consistent quality of the raw materials, which undergo rigorous evaluation to assess their chemical composition and physical properties. This meticulous scrutiny is imperative to ensure that the final grinding balls meet stringent specifications and standards.
Melting and Molding:
Upon obtaining the raw materials, they undergo a transformative process within a high-temperature furnace, typically reaching temperatures around 1450°C. The intense heat causes the raw materials to melt and form a molten metal, which is then carefully poured into specialized molds. These molds are intricately designed to impart uniformity in size and shape to the grinding balls, laying the foundation for their exceptional performance in grinding applications.
Heat Treatment for Enhanced Performance:
Following the solidification of the molten metal, the formed grinding balls undergo a series of crucial heat treatment processes, including quenching and tempering. Quenching involves rapidly cooling the balls to elevate their hardness, while tempering serves to reduce brittleness and enhance toughness. These meticulously orchestrated heat treatment procedures are pivotal in augmenting the wear resistance and impact strength of the grinding balls, thereby ensuring their longevity and reliability in diverse grinding applications.
Precision Machining Operations:
Post heat treatment, the grinding balls progress through precision machining operations, including grinding and polishing, to achieve their final dimensions and impeccable surface finish. These meticulous techniques are employed to meticulously attain the specified tolerances and quality standards, ensuring that each grinding ball possesses uniformity in size, shape, and surface attributes. This precision is instrumental in optimizing the grinding performance of the balls across varied applications.
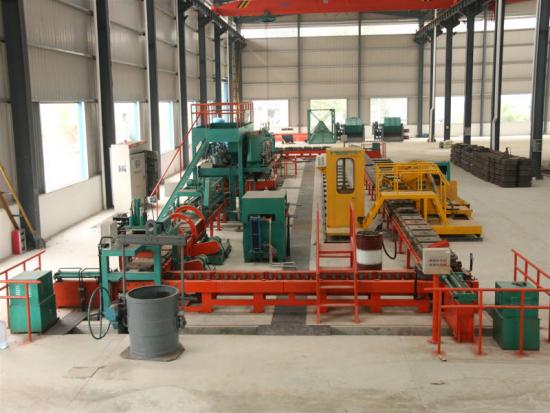
Stringent Quality Inspection:
Throughout the manufacturing process, stringent quality control measures are steadfastly upheld. Once the machining operations are completed, the grinding balls undergo meticulous inspections to detect any imperfections or irregularities. Dimensional measurements, hardness testing, and comprehensive visual inspections are meticulously conducted to validate adherence to exacting criteria, ensuring that only flawless grinding balls advance to the subsequent stages of production.
Packaging and Preparation for Dispatch:
Upon successful completion of the rigorous inspection process, the approved grinding balls are meticulously sorted based on size and quality to meet the specific requirements of discerning customers. Subsequently, the grinding balls are expertly packaged and prepared for shipping, ensuring the secure and reliable transit of these precision-crafted components to their intended destinations, where they stand poised to deliver superior grinding performance.
The manufacturing process of grinding balls epitomizes a symphony of precision and meticulousness, encompassing the sourcing of raw materials, melting and molding, heat treatment, precision machining, stringent quality inspections, and meticulous packaging. Each stage is meticulously executed to ensure the creation of superior-quality grinding balls that align with exacting specifications and standards. By upholding unwavering commitment to quality control, manufacturers can furnish industries with grinding balls that embody unrivaled reliability and efficacy in diverse grinding applications.
As we unravel the complex manufacturing process of grinding balls, the precision and craftsmanship involved become evident. The production of grinding balls is a highly specialized endeavor that demands meticulous attention to detail, quality control, and cutting-edge technology. At Zhicheng , we take pride in being a leading manufacturer and exporter of grinding ball production equipment. With our dedication to providing professional products and export services, we assure you of the most competitive pricing and superior product quality in the market.
Zhicheng is committed to offering state-of-the-art manufacturing equipment that ensures the efficient and precise production of grinding balls. Our expertise in this field enables us to meet the stringent demands of the industry while delivering products of the highest standards. Get in touch with us to explore our range of grinding ball production equipment and experience the difference our professional products and export services can make.