Grinding balls play a critical role in a variety of industrial applications, particularly in industries that rely on mills for grinding materials. These industries include mining, cement production, and various types of material processing. In this article, we will explore the purpose of grinding balls, their uses, the materials they are made from, and their importance in various industrial processes.
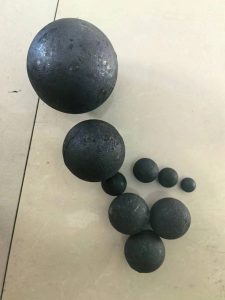
What Are Grinding Balls?
Grinding balls are spherical or ball-shaped materials used in grinding mills to crush and reduce the size of materials, such as ores, minerals, and other substances. These balls are an essential part of the grinding process, facilitating the reduction of larger particles into smaller, more manageable sizes.
In grinding mills, such as ball mills, rod mills, or SAG mills (semi-autogenous grinding mills), grinding balls are fed into the mill alongside the raw materials. As the mill rotates, the grinding balls move with the material, exerting pressure and impact, which gradually breaks down the material.
What Is the Purpose of Grinding Balls?
The primary purpose of grinding balls is to reduce the size of materials through mechanical impact, abrasion, and grinding. In most cases, grinding balls work by striking the raw material and applying sufficient pressure to break down larger particles into smaller sizes. This is particularly important in industries such as mining and cement production, where raw materials must be finely ground for further processing.
Here are the key purposes of grinding balls:
1. Material Size Reduction
The primary function of grinding balls is to facilitate size reduction in mills. By continuously impacting the raw material, grinding balls reduce large particles into smaller ones. This process is vital in industries where raw materials need to be finely ground to produce end products like cement, minerals, and metals.
2. Achieving Uniform Particle Size Distribution
In many industries, achieving a uniform particle size distribution is critical to the quality of the final product. Grinding balls help in achieving this uniformity by continuously grinding and mixing the material as it is processed in the mill. This is essential for producing high-quality products that meet specific standards and specifications.
3. Enhancing Grinding Efficiency
The presence of grinding balls helps to increase the overall efficiency of the grinding process. They maximize the impact force on the material, ensuring that particles are crushed and reduced to the desired size. The grinding process would be much slower and less efficient without the use of grinding balls.
4. Reducing Energy Consumption
Using grinding balls can help optimize energy consumption in the grinding process. The balls are designed to efficiently break down material with minimal energy use. High-quality grinding balls can extend the life of the mill and reduce energy consumption, making the entire grinding process more cost-effective and sustainable.
What Are the Different Types of Grinding Balls?
Grinding balls are manufactured from a variety of materials, and the type of material used depends on the specific application. Some of the most common materials used to make grinding balls include:
1. Steel Balls
Steel balls are the most common type of grinding balls. They are typically made from high-carbon steel, chrome steel, or alloyed steel, which makes them durable and resistant to wear and tear. Steel balls are widely used in industries such as mining, cement, and chemical processing.
2. Cast Iron Balls
Cast iron grinding balls are used in industries where cost is a significant factor. They are made from molten iron and then cast into spherical shapes. Cast iron balls are durable and have good wear resistance but are generally not as strong as steel balls, making them more suitable for specific applications.
3. Ceramic Balls
Ceramic grinding balls are made from advanced ceramics such as alumina, zirconia, or silicon carbide. These balls are known for their excellent wear resistance, high strength, and low density. Ceramic balls are often used in specialized grinding applications where contamination must be avoided, such as in the production of pharmaceuticals, food, or high-precision materials.
4. Forged Steel Balls
Forged steel grinding balls are produced through a process of heating and forging steel. This method gives the balls enhanced strength and resistance to wear. Forged steel balls are typically used in heavy-duty grinding applications and are ideal for industries such as mining, cement, and power generation.
5. Glass Balls
Glass grinding balls are used in industries where contamination must be minimized, such as in the food and pharmaceutical sectors. These balls are made from various types of glass and are highly resistant to corrosion, making them ideal for grinding non-ferrous materials.
What Are the Key Applications of Grinding Balls?
Grinding balls have a wide range of applications in various industries. Some of the most common applications include:
1. Mining and Mineral Processing
In the mining industry, grinding balls are used to reduce the size of mined ores. The grinding process is essential for extracting valuable minerals, such as gold, copper, and iron. Grinding balls help in breaking down large pieces of ore into smaller, more manageable sizes for further processing and refining.
2. Cement Production
In the cement industry, grinding balls are used to grind raw materials like limestone, clay, and gypsum into a fine powder, which is then used to produce cement. The efficiency of the grinding process is critical in cement production, as it directly impacts the final quality of the cement.
3. Chemical Processing
Grinding balls are also used in chemical processing to grind raw materials, such as pigments, chemicals, and other substances, into fine powders. The precise control of particle size is essential in ensuring the consistency and quality of the final chemical products.
4. Power Generation
In power plants, grinding balls are used in mills that grind coal and other fuels into smaller particles for combustion. The size of the coal particles directly affects the efficiency of the combustion process, making the use of grinding balls crucial for maximizing energy output.
5. Food and Pharmaceutical Industries
In the food and pharmaceutical industries, grinding balls are used to achieve fine particle sizes in the production of various products, including medicines, spices, and food ingredients. Ceramic and glass balls are often used in these industries due to their ability to prevent contamination and maintain hygiene standards.
What Are the Benefits of Using Grinding Balls?
The use of grinding balls in industrial processes offers several key benefits, including:
- Increased Productivity: By ensuring a more efficient grinding process, grinding balls help industries achieve higher productivity and reduced downtime.
- Improved Quality: The reduction in particle size and uniformity of the grind ensures higher-quality final products.
- Cost Efficiency: High-quality grinding balls contribute to a more energy-efficient and cost-effective grinding process, ultimately reducing operational costs.
- Longevity: Using durable grinding balls, such as forged steel or ceramic balls, ensures long-lasting performance, reducing the need for frequent replacements.
Conclusion
Grinding balls are essential components in a variety of industrial applications, playing a critical role in size reduction, enhancing grinding efficiency, and ensuring the quality of the final product. The materials from which they are made, such as steel, cast iron, and ceramics, are selected based on the specific needs of the application, ensuring maximum performance and durability. Whether in mining, cement production, or the pharmaceutical industry, grinding balls help to optimize production processes, reduce energy consumption, and improve product quality, making them indispensable in modern industrial operations.